Revolutionizing Utility Vehicles:
JAC Introduces Advanced Digital Manufacturing System in Australia
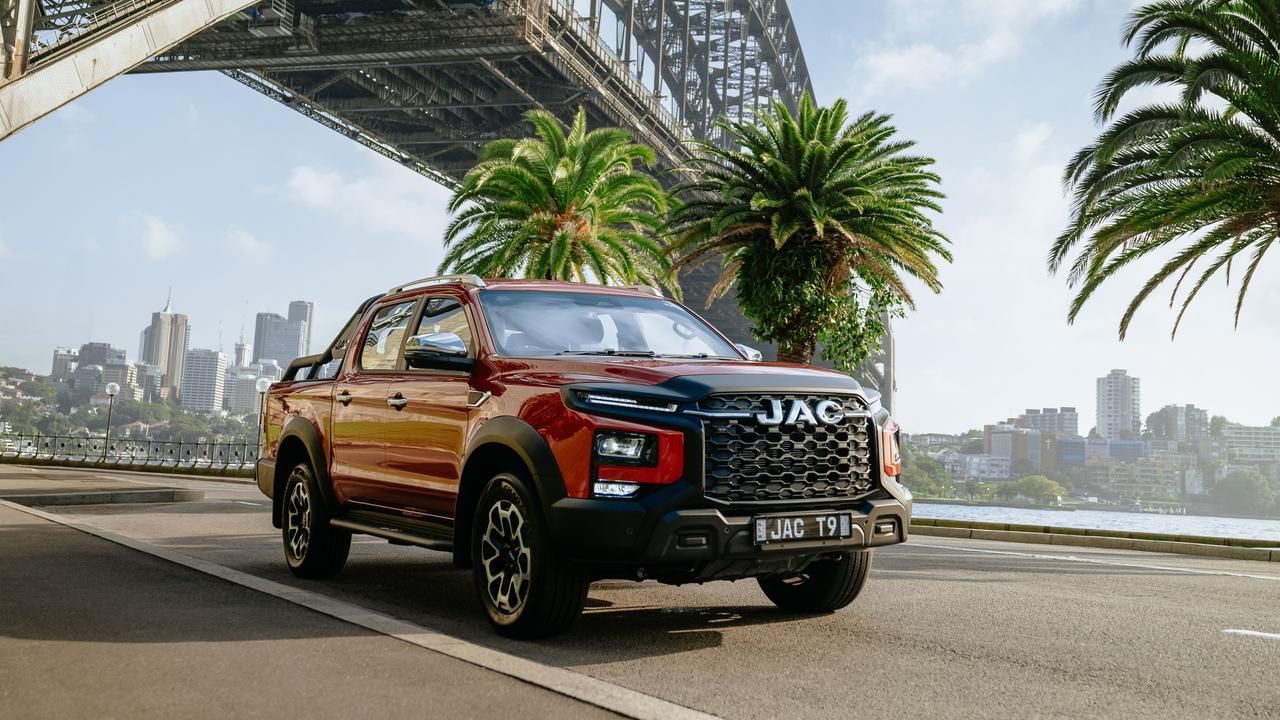
In the ever-evolving automotive industry, innovation continues to be the driving force behind the success of new vehicles entering the market. As Australia eagerly anticipates the arrival of the latest offering from Chinese brand JAC, the T9 utility vehicle, excitement is brewing over the introduction of a groundbreaking Digital Manufacturing System (DMS). Set to be only the second Ute equipped with this cutting-edge technology, the T9 promises to revolutionize the landscape of utility vehicles in Australia.
Imported by LTS Auto, the T9 boasts exceptional features designed to enhance both safety and efficiency on the road. One of the standout features of this vehicle is its Driver Monitoring System (DMS), a sophisticated technology that utilizes advanced sensors to detect when the driver's attention drifts away from the road. This innovative system serves as a crucial safety measure, providing alerts and interventions if it detects signs of drowsiness or distraction, ultimately reducing the risk of accidents and ensuring a safer driving experience for all.
However, what truly sets the T9 apart is its integration of a Digital Manufacturing System (DMS) into the production process. As the second Ute to incorporate this state-of-the-art technology, the T9 represents a significant leap forward in manufacturing excellence. Here are three key elements that highlight the transformative impact of the DMS on the production of the T9:
1. Integration with Vehicle Design and Production: The implementation of a Digital Manufacturing System (DMS) allows for seamless integration with the design and production process of the T9. Through digital modeling, simulation, and prototyping, manufacturers can fine-tune every aspect of the vehicle's design, ensuring optimal performance and quality. By leveraging advanced digital technologies, the production process becomes more efficient and cost-effective, ultimately leading to a superior end product.
2. Data Analytics and Real-time Monitoring: With the DMS in place, real-time monitoring of the manufacturing process becomes a reality. By gathering data from sensors and machinery on the production floor, manufacturers can analyze performance metrics, identify potential bottlenecks, and predict maintenance needs. This data-driven approach enables proactive decision-making, allowing for adjustments to be made in real-time to optimize efficiency and minimize downtime.
3. Automation and Robotics: The integration of automation and robotics within the Digital Manufacturing System (DMS) significantly enhances the production process of the T9. Automated assembly lines, robotic arms, and autonomous guided vehicles (AGVs) work in tandem to streamline manufacturing operations, reducing the reliance on manual labor and improving overall efficiency. By harnessing the power of automation, manufacturers can achieve higher levels of precision and consistency, resulting in a superior quality product.
As JAC prepares to introduce the T9 utility vehicle to the Australian market, anticipation is building over the potential impact of its advanced Digital Manufacturing System (DMS). With its innovative features, including the Driver Monitoring System (DMS) and upcoming hybrid version, the T9 represents a bold step forward in automotive technology. By embracing cutting-edge digital manufacturing processes, JAC is poised to set a new standard for excellence in the utility vehicle segment, cementing its reputation as a leader in innovation and quality.
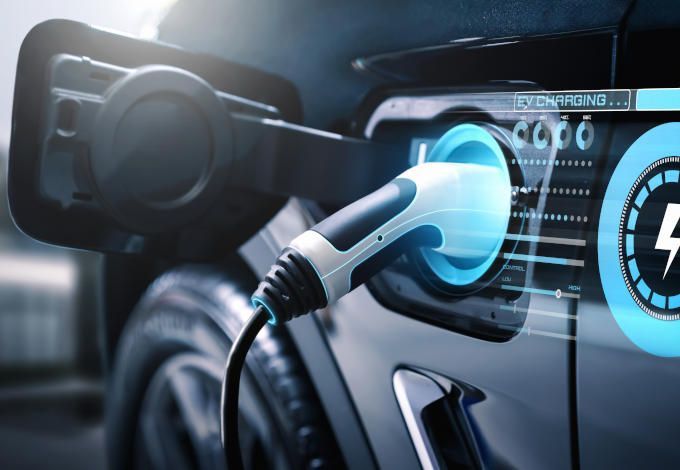
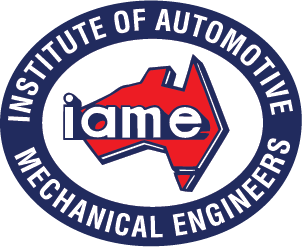